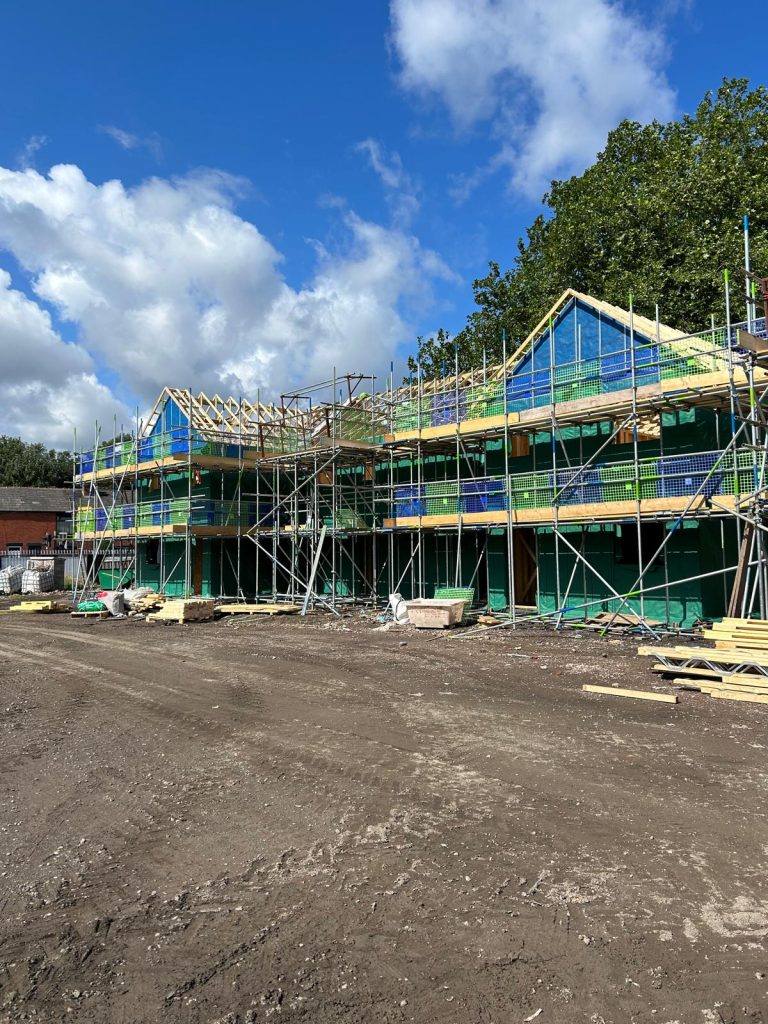
- Production and Building Time
Manufacturing of the closed panel timber frames may begin promptly upon receipt of approval for the fabrication designs, as they are made within our own plant. It takes 8-10 weeks for us to design, engineer, and manufacture all the frames, including ordering any structural elements and fittings, after our clients accept our price. We then arrange for their direct delivery to the site.
You may expect a fully waterproof structure after the frames are on site, which should take about two to three weeks depending on the final design specifications. The rapid return on investment and more specific timetables made possible by closed panel construction make it an excellent choice for budgeting.
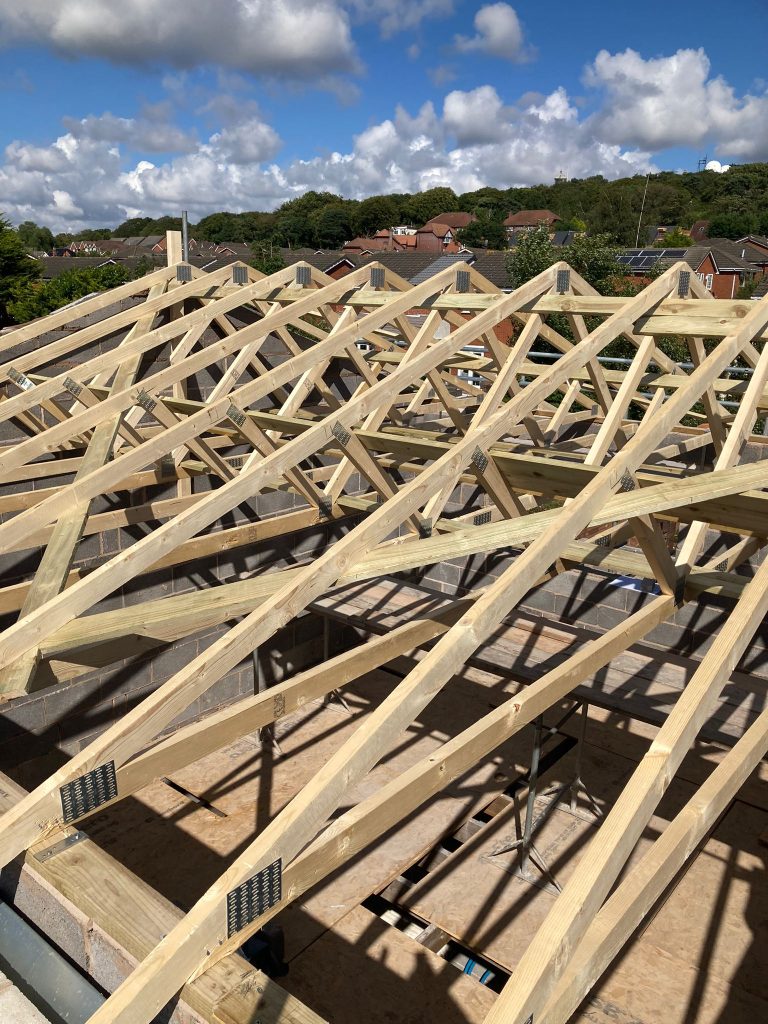
- First Fix Services Are A Piece of Cake – Access Wise
Plumbers and electricians can easily access the service void within the panels to do their first fix, which will help save their time on site and costs. In addition to this, the panels’ thermal performance is enhanced by the service void. In addition to providing sufficient space for pipes and cables, our movable metal web joist design makes it easy for tradespeople to access the walls and floors.
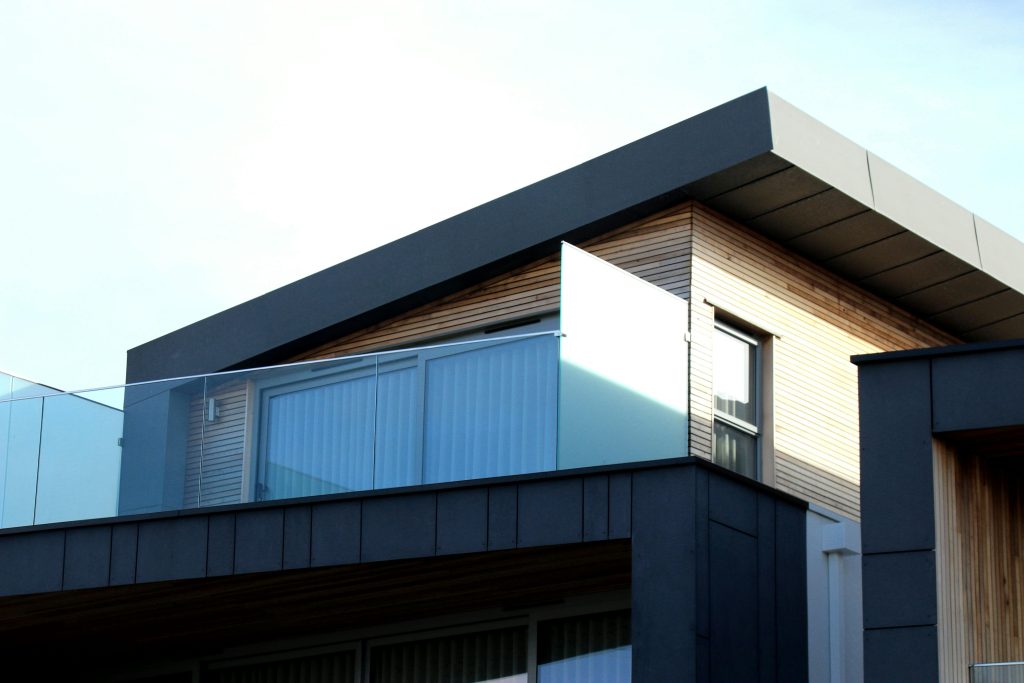
- ENTIRELY CRAFTED IN A MONITORED FACTORY
This guarantees that the panels are of the greatest quality in every respect. After being assembled into the timber frame in the factory, the vapour control foil, breather membrane, insulation, and high performance fibre board are then covered in protective plastic and transported to the site by lorry. A fully weatherproof and structurally sound building, ready for both interior and exterior finishing, is what they deliver to clients.
Here is a picture of our plant where we make closed panels like the ones mentioned earlier. You can also see them being loaded into a truck to be delivered to the site.
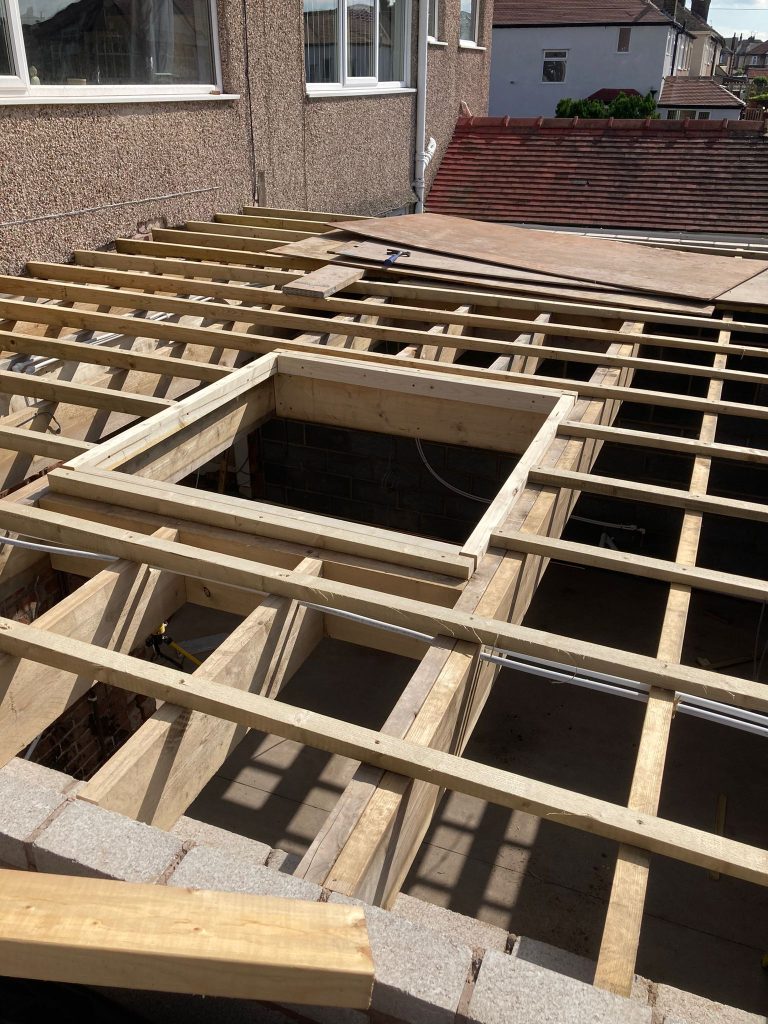
- Minimised Waste on Site
There is a significant decrease in on-site waste because the panels are made entirely in a facility. lumber is an infinitely renewable resource because it is organic, non-toxic, and can be burned for electricity or converted into something else entirely if there is any waste lumber on site.
this are some images from one of our projects; after the closed panels are assembled, there is very little waste on the site, and this is how they appear once they are up…
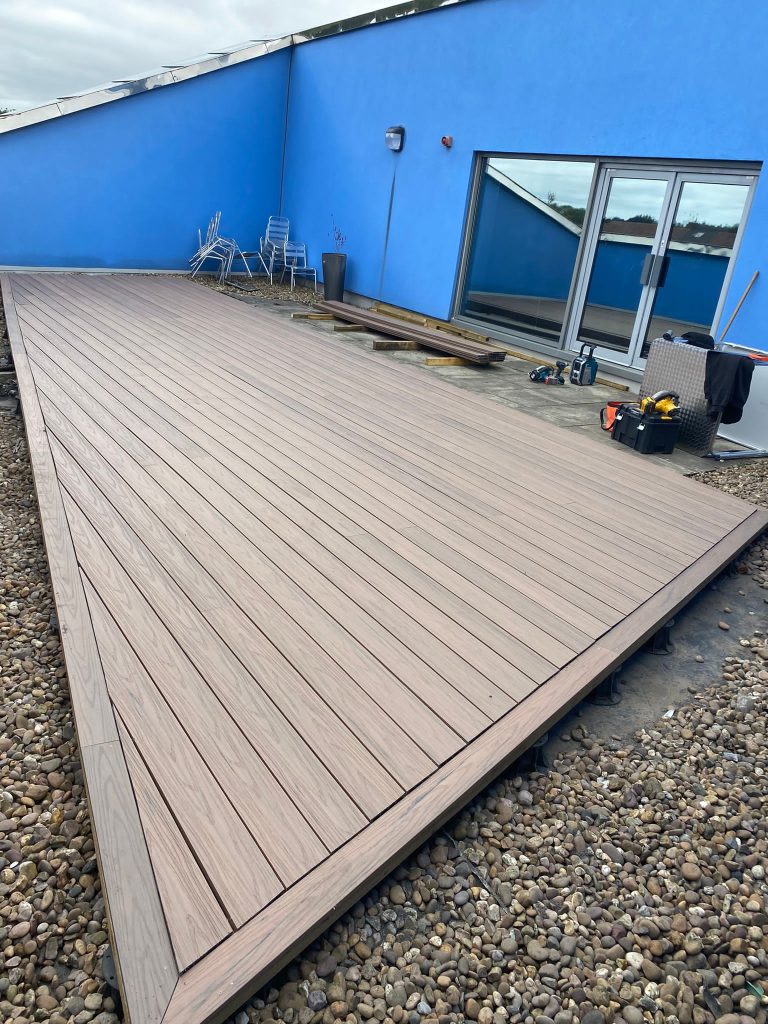
- PROFESSIONAL FIBRE BOARD
In addition to being applied to both sides of the inside walls, Fermacell Board is also applied to the inside of the exterior panels. Fermacell has exceptional resistance to fire, impact, racking, and moisture, in addition to being soundproof. It works effectively for off-site fabrication, which cuts down on construction time and waste.
Without the need for noggins, you may fix anything from kitchen cabinets to exercise equipment directly to the board thanks to the board’s strength, which permits load weights of up to 50 kg per cavity fastening and 30 kg per screw. Quicken the building process by decorating straight onto the board with paint, wallpaper or tiles; if painting, skim for a smoother surface.
A shorter build time and less money spent on extras like plasterers are both achieved by using the board that is pre-fitted in our manufacturing.
We are proud of our services, their sustainability and the value for our customers. If you would like to enquire further, please get in touch on our Contact Us page.